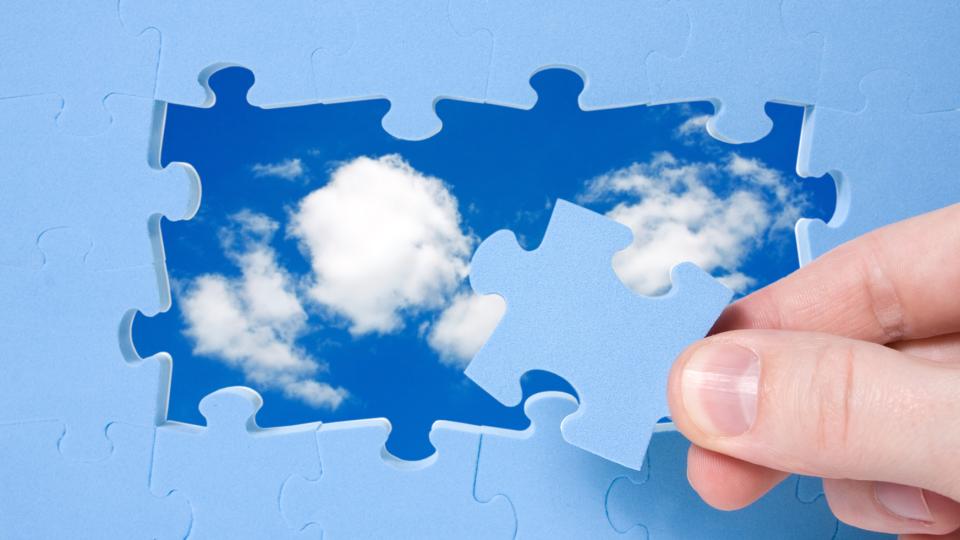
Dritte Runde des Innovationswettbewerbs Industrie.IN.NRW: 23 zukunftsweisende Projekte zur Förderung vorgeschlagen
Die dritte Einreichungsrunde des Innovationswettbewerbs „Industrie.IN.NRW“ ist erfolgreich abgeschlossen: Ein unabhängiger Begutachtungsausschuss hat 23 besonders vielversprechende Vorhaben zur Antragstellung vorgeschlagen. Für die Umsetzung der ausgewählten Projekte stehen rund 34,9 Millionen Euro Fördermittel des Landes Nordrhein-Westfalen und der EU aus dem Europäischen Fonds für regionale Entwicklung (EFRE) bereit. Der Innovationswettbewerb „Industrie.IN.NRW“ wird im Rahmen des EFRE/JTF-Programms NRW 2021–2027 vom Ministerium für Wirtschaft, Industrie, Klimaschutz und Energie in Zusammenarbeit mit dem Ministerium für Kultur und Wissenschaft sowie dem Ministerium für Umwelt, Natur- und Verbraucherschutz des Landes Nordrhein-Westfalen umgesetzt. Ziel ist, die Schlüsselbereiche Werkstoffe und Produktion zu unterstützen.
Wirtschaftsministerin Mona Neubaur: „Die aktuellen weltwirtschaftlichen Spannungen und Handelskonflikte machen deutlich, wie wichtig es ist, dass wir in Nordrhein-Westfalen, Deutschland und Europa aus eigener Innovationskraft Stärke und Unabhängigkeit entwickeln. Gerade unsere kleinen und mittleren Unternehmen zeigen dabei immer wieder, wie viel Erfindergeist, Lösungsorientierung und Mut zur Veränderung in ihnen steckt. Die große Resonanz auf den Wettbewerb und die Qualität der Projektideen sind ein starkes Signal für die Innovationskraft unseres Industriestandortes. Nordrhein-Westfalen ist bereit, die digitale und nachhaltige Transformation mitzugestalten – und sich mit innovativen Lösungen international zu behaupten.“
Umweltminister Oliver Krischer: „Mit dem Wettbewerb Industrie.IN.NRW stärken wir die Wirtschaft in Nordrhein-Westfalen. Zugleich fördern wir eine umweltfreundlichere Industrie. Die eingereichten Projektideen zeigen, wie viel Erfindergeist in unseren Unternehmen steckt. Dieses Potenzial ist der Schlüssel, um Klimaschutz und wirtschaftlichen Fortschritt gemeinsam zu gestalten.“
Wissenschaftsministerin Ina Brandes: „Nordrhein-Westfalen hat ein europaweit einmalig dichtes Netz von Hochschulen und Forschungseinrichtungen. Hier finden Unternehmen ein hervorragendes Umfeld, das sie für marktfähige Innovationen brauchen. Mit ‚Spitzenforschung made in NRW‘ und starken Partnern in der Industrie finden kluge Ideen ihren Weg in die Anwendung – auch im großindustriellen Maßstab.
Industrie.IN.NRW zeigt eindrucksvoll, wie viel Innovationskraft im Wissenschafts- und Wirtschaftsstandort Nordrhein-Westfalen steckt.“
Der Innovationswettbewerb unterstützt gezielt die strategische technologische Weiterentwicklung in Nordrhein-Westfalen mit Fokus auf die Schlüsselbereiche Werkstoffe und Produktion. Gefördert werden vorrangig kleine und mittlere Unternehmen (KMU) in Zusammenarbeit mit Wissenschaft und Forschung, um innovative, nachhaltige und wettbewerbsfähige Lösungen zu entwickeln. Ziel ist es, die digitale und nachhaltige Transformation voranzutreiben sowie wirtschaftliches Wachstum, Beschäftigung und Innovationskraft in Nordrhein-Westfalen und die strategische Unabhängigkeit Europas zu stärken. Alle geförderten Vorhaben stehen im Einklang mit der Regionalen Innovationsstrategie NRW.
Mit dem erfolgreichen Abschluss der dritten Einreichungsrunde wurden im Rahmen des Wettbewerbs insgesamt 55 Projekte mit einer Fördersumme von insgesamt 87,4 Millionen Euro auf den Weg gebracht.
Geförderte Vorhaben der dritten Runde:
UltrasonAIc – AI based Ultrasonic Testing System for Real-Time Defect Detection
Im Projekt soll ein KI-gestütztes Assistenzsystem für die Ultraschallprüfung von Schweißnähten entwickelt werden. Diese Lösung soll eine umfassende Qualitätskontrolle sicherheitsrelevanter Bauteile ermöglichen. Hierzu werden unter anderem KI-Modelle eingesetzt, die die Fehlererkennung in Echtzeit verbessern sollen.
Projektpartner sind die deeplify GmbH (Bochum), die Bundesanstalt für Materialforschung und -prüfung BAM (Berlin) und die DGZfP Ausbildung und Training GmbH (Dortmund).
FeNCy-PEM – Herstellung und Einsatz von edelmetallfreien Fe-N-C-Katalysatoren
Ziel des Projekts ist die Herstellung edelmetallfreier Katalysatoren für PEM-Brennstoffzellen. Im Fokus stehen die Entwicklung eines kontinuierlichen, skalierbaren Produktionsprozesses, die Integration in die Fertigung und die Anwendung in Brennstoffzellensystemen.
Projektpartner sind das Institut für Umwelt & Energie, Technik & Analytik e. V. (Duisburg), die IPLAS Innovative Plasma Systems GmbH (Troisdorf), die Westfälische Hochschule (Gelsenkirchen), die ZBT - Zentrum für Brennstoffzellen-Technik GmbH (Duisburg) und die Laufenberg GmbH (Krefeld).
WISES – Vorausschauende Wartung in der Industrie zur Steigerung der Verfügbarkeit und Energieeffizienz mittels multimodaler Analysemodelle und agenten-geführter mobiler Sensorik
Im Projekt soll die vorausschauende Wartung von Maschinen und Anlagen in der Industrie durch multimodale Analysemodelle und zugehörige Entscheidungsalgorithmen verbessert werden. Die Erkennung von Anomalien soll dabei mit mobiler Sensorik erfolgen. Aus den erkannten Anomalien sollen zugehörige Wartungsempfehlungen abgeleitet werden.
Projektpartner sind die Universität Siegen (Siegen), die U-Glow GmbH (Mülheim an der Ruhr), die ifm electronic GmbH (Essen) und die Nagels Druck Kempen GmbH (Kempen).
FAiL – Fehleranalyse und Auswirkung in großformatigen Lithium-Ionen-Batterien
Ziel des Projekts ist, die Auswirkung von kritischen Produktionsfehlern auf die Sicherheit und Leistungsfähigkeit von Lithium-Ionen-Batterien quantitativ zu bewerten, um Ursache-Wirkungs-Zusammenhänge zu ermitteln. Hierzu werden großformatige Batterien in unterschiedlichen Zellformaten mit definierten Fehlerbildern sowie entsprechende Referenzzellen elektrochemisch analysiert.
Projektpartner sind die Fraunhofer-Einrichtung Forschungsfertigung Batteriezelle FFB (Münster), die Protec-24 facility service GmbH (Unna), die diondo GmbH (Hattingen), die ACCURE Battery Intelligence GmbH (Aachen) und das Fraunhofer-Institut für Solare Energiesysteme ISE (Freiburg im Breisgau).
LeiBat – Entwicklung und Herstellung eines recyclingfreundlichen Leichtbau-Hybrid-Batteriegehäuses
Ziel des Projekts ist die Entwicklung eines neuartigen Batteriegehäuses, welches mehr Bauraum für Batteriezellen aufweist. Durch den Einsatz neuer Fertigungsverfahren und Multi-Materialsysteme sollen dabei Kosten und Gewicht reduziert werden. Hierdurch soll eine höhere Reichweite von batteriebetriebenen Fahrzeugen ermöglicht und zugleich eine hohe Recyclingfähigkeit gewährleistet werden.
Projektpartner sind die Universität Siegen (Siegen), die Kunststofftechnik Backhaus GmbH (Kierspe), die Erwin Quarder Systemtechnik GmbH (Espelkamp), die Weber Fibertech GmbH (Markdorf) und die Röttger GmbH & Co. KG (Marienheide).
DIMANENT – Digitale Multimediale Anleitungen Erstellen und Nutzen
In DIMANENT soll eine KI-basierte Software entwickelt werden, die es ermöglicht, digitale dynamische Bedienungsanleitungen aufwandsarm und zuverlässig zu erstellen. Hierzu wird ein Methodenbaukasten entwickelt, der ein Wissensmanagementsystem, einen Konfigurator für die digitale Darstellungsform oder Sprachmodelle zur Erstellung von neuen maschinenspezifischen Texten enthält.
Projektpartner sind das Fraunhofer-Institut für Optronik, Systemtechnik und Bildauswertung IOSB-INA (Lemgo), die Wöhler Brush Tech GmbH (Bad Wünnenberg), die Smartsquare GmbH (Bielefeld), die Anlagenbau Habeck GmbH & Co. KG (Ostercappeln) und die SALZ Automation GmbH (Bad Salzuflen).
NAPPA – Nanolegierungen aus Metallpulvern hergestellt im Mikrowellenplasma für die A-EM-Elektrolyse
Das Projekt zielt mittels der Entwicklung innovativer Katalysatormaterialien darauf ab, die Anionenaustauschmembran-Elektrolyse (AEM-EL) als kostengünstige und skalierbare Technologie für die grüne Wasserstoffproduktion zu etablieren. Hierzu sollen innovative Katalysatormaterialien entwickelt werden, die einen Verzicht auf kritische Rohstoffe (Nickel, Kobalt) ermöglichen.
Projektpartner sind das Institut für Umwelt & Energie, Technik & Analytik e. V. (Duisburg), das Forschungszentrum Jülich GmbH - Institute for Energy Technologies (Jülich), die xemX materials space exploration GmbH (Bochum) und die Kamp & Kötter GmbH (Bochum).
CableSmith – Entwicklung eines Seilroboters zur Automatisierung der Schmiedeprozesse bei mittleren Losgrößen
Ziel des Projekts ist die Entwicklung eines Seilroboters, der ohne infrastrukturelle Maßnahmen in bestehende Produktionsstraßen integriert werden kann. Durch die vollständige Automatisierung der Programmierung soll der Seilroboter ohne Programmierkenntnisse betrieben werden können. Durch das gesteigerte Automatisierungsniveau soll die Wettbewerbsfähigkeit von kleinen und mittelständischen Schmiedeunternehmen gesteigert werden.
Projektpartner sind die red cable robots GmbH (Duisburg), die machineering GmbH & Co. KG (München), die IconPro GmbH (Aachen), die Fachhochschule Südwestfalen, Labor für Massivumformung LFM (Iserlohn) und die Fachhochschule Südwestfalen, Labor für Automatisierungstechnik und lernende Systeme ALS (Iserlohn).
OptimizationChat – Mathematische Optimierung auf Basis natürlichsprachlicher Interaktion: Industrierelevante Probleme formalisieren und lösen
Das Projekt zielt darauf ab, Optimierungsprobleme der industriellen Produktion durch ein Chatsystem zu identifizieren. Diese sollen durch eine mathematische Formalisierung des zugrundeliegenden Optimierungsproblems aus einem natürlich-sprachlichen Dialog mit dem Benutzer abgeleitet werden.
Projektpartner sind das Fraunhofer-Institut für Optronik, Systemtechnik und Bildauswertung IOSB-INA (Lemgo), die Universität Bielefeld (Bielefeld), die Databay AG (Würselen), die Digital Twin Factory GmbH (Bad Oeynhausen) und die OPTANO GmbH (Paderborn).
DIGI4PLAS – Neue digitale Methoden zur Optimierung und Steuerung von Plasmabeschichtungsprozessen in der Produktion
Das Projekt zielt darauf ab, industrielle Produktionsprozesse durch den Einsatz von KI und innovativen Messtechniken zu optimieren. Die Kombination dieser Technologien soll eine kontinuierliche Überwachung und Steuerung von Plasmaproduktionsprozessen ermöglichen, die in verschiedenen Oberflächenbehandlungen genutzt werden.
Projektpartner sind die House of Plasma GmbH (Bochum), die deeplify GmbH (Bochum), das Fraunhofer-Institut für Schicht- und Oberflächentechnik IST (Braunschweig) und die PLASUS GmbH (Mering).
3DCeraTex – Entwicklung einer modularen 3D-Flechtanlage für faserverstärkte keramische Composite-Bauteile mit Auslegungssoftware über Multiskalensimulation
Ziel des Projekts ist die Entwicklung einer modularen Flechtanlage mit elektrischen, kraftgeregelten Klöppeln und unabhängigen Trajektorien der Klöppel, was erstmals ein Flechten von keramischen Fasern mit variablen 3D-Flechtmustern auch innerhalb eines Bauteiles ermöglicht.
Projektpartner sind die DIRKRA Sondermaschinenbau GmbH & Co.KG (Stolberg), die inuTech GmbH (Nürnberg) und das Institut für Unternehmenskybernetik e.V. (Aachen).
TiMM – Entwicklung eines disruptiven Herstellungsverfahrens für Titanlegierungen mittels metallothermischer, selbstausbreitender Hochtemperatursynthese und Upcycling von Pulverabfällen der metallischen additiven Fertigung
Ziel des Projekts ist die Entwicklung eines Verfahrens zur einstufigen Erzeugung von Titan(vor)legierungen unter Zugabe von bisher nicht-recycelbarem Titanpulver aus dem 3D-Druck. Die Innovation liegt in der Kombination von aluminothermischen Reaktionen (selbstausbreitende Hochtemperatursynthese zur Aufschmelzung und Homogenisierung von Titanerz und Legierungskomponenten) mit zentrifugalen Fliehkräften zur beschleunigten Trennung von Schlacke und Legierung.
Projektpartner sind die ManVision GmbH & Co. KG (Hemer) und die Technische Universität Bergakademie Freiberg (Freiberg).
ProFlex – Entwicklung intelligenter Produktionsprozesse für eine innovative flexible Antriebswelle auf Basis neuartiger Materialkombinationen zur signifikanten Steigerung des Marktpotenzials
Im Projekt soll ein optimierter Fertigungsprozess für lange, biegesteife Wellen entwickelt werden, mit dem relevante Marktsegmente im maritimen Bereich erschlossen werden können. Zusätzlich soll ein hoch automatisierbares, kostengünstiges Fertigungsverfahren entwickelt werden, das (basierend auf neuen Materialkombinationen) einen Einstieg in den industriellen Massenmarkt ermöglicht.
Projektpartner sind die NEMOS GmbH (Duisburg), die Universität Duisburg-Essen (Duisburg) und die Stüwe GmbH & Co. KG (Hattingen).
DirekTief
In diesem Projekt soll ein neues, innovatives Tiefbohrverfahren entwickelt werden, mit dem die Qualität, die Geschwindigkeit und die Genauigkeit beim Tieflochbohren deutlich verbessert werden, da das traditionelle Tiefbohren durch bestimmte Durchmesser- und Tiefenverhältnisse in seiner Genauigkeit eingeschränkt ist.
Projektpartner sind die Fraunhofer-Einrichtung für Energieinfrastrukturen und Geotechnologien IEG (Bochum), die Befeld Präzisionstechnik GmbH (Bochum), die Seco Tools GmbH (Erkrath), die IRLE ROLLS GmbH (Netphen) und die ISBE GmbH (Stuttgart).
PROGRESS-PEMEL – Projekt zur Entwicklung eines Fertigungsprozesses für eine Rolle-zu-Rolle-Gestaltung von ressourcenschonenden, effizienten PEM-Wasserelektrolyse-Systemen
Ziel des Projekts ist die Entwicklung neuer Materialien und Verfahren, um katalysatorbeschichtete Membranen ressourcenschonend und kostengünstig im industriellen Maßstab herzustellen. Im Mittelpunkt steht ein nachhaltiges Decal-Transferverfahren, bei dem eine galvanisch abgeschiedene Katalysatorschicht zunächst auf elektrisch leitfähige Supportmaterialien und anschließend auf eine Membran übertragen wird.
Projektpartner sind die Hydrogenea GmbH (Gelsenkirchen), die Westfälische Hochschule Gelsenkirchen Bocholt Recklinghausen (Gelsenkirchen), die HSWmaterials GmbH (Kamp-Lintfort) und das Zentrum für Brennstoffzellen-Technik GmbH ZBT (Duisburg).
FGL-MEX – Ressourcenschonende hybride Fertigung eines Aktors mit Formgedächtnislegierung unter Verwendung der Materialextrusion
In FGL-MEX soll eine neue Prozesstechnologie entwickelt werden, um Formgedächtnislegierungen bei additiver Fertigung bereits im Druckprozess mechanisch und elektrisch in ein Aktorgehäuse einzubinden. Hierzu soll ein bestehender Fertigungsprozess, das Crimpen, vollständig substituiert werden. Dies dient dazu, diese Aktortechnologie für breitere industrielle Anwendungen markt- und wettbewerbsfähig zu machen.
Projektpartner sind die Kunststoffverarbeitung Hoffmann GmbH (Heiligenhaus) und die Universität Duisburg-Essen (Duisburg).
ReduFaWeIn – Werkzeugstrukturen und -beschichtungen zur Reduzierung von Farbwechselintervallen in Blasformprozessen
Im Projekt ReduFaWeIn wird eine innovative, neue Oberflächenstrukturierung in Kombination mit moderner Beschichtungstechnologie entwickelt, welche einen beschleunigten Farbwechsel in Extrusions-Blasformprozessen ermöglichen soll.
Projektpartner sind die gemeinnützige KIMW Forschungs-GmbH (Lüdenscheid), die Dreistegen GmbH (Monschau) und die W. Müller GmbH (Troisdorf).
AutoSim – Automatisierte, effiziente Erstellung von Simulationsmodellen für industrielle Anwendungen
In AutoSim soll ein System entwickelt werden, welches die effiziente, automatisierte Erstellung von Simulationsmodellen für die Industrie ermöglicht. Hierzu werden 3D-Scans von Produktionsstandorten verwendet, die durch KI-basierte Analysen in Segmentierung und Klassifikation der Maschinen und Anlagen mündet. Ziel ist es, den Modellierungsprozess zu beschleunigen und so Produktionsplanung, Optimierung und Automatisierung zu ermöglichen.
Projektpartner sind die RWTH Aachen (Aachen) und die RIIICO GmbH (Düsseldorf).
Digital Low Emission Brake
Im Projekt sollen neue Legierungen zur Hartstoffbeschichtung von Bremsscheiben entwickelt werden. Diese sollen einen verringerten Abrieb ermöglichen, sodass längere Standzeiten erreicht werden und Bremsstaub reduziert wird.
Projektpartner sind die RWTH Aachen (Aachen), die GOTEC Brake Disc Coatings GmbH (Wülfrath), die ThetaScan GmbH (Dinslaken) und die HPL Technologies GmbH (Alsdorf).
SPEED4REMAN
Ziel des Projekts ist die Erarbeitung von Prozessstrukturen und Workflows, die eine Ausweitung des Remanufacturing-Geschäfts im Bereich von LKW ermöglichen. Die technischen und wissenschaftlichen Aufgabenstellungen befinden sich im Bereich der dynamischen Prozessabbildung, der Digitalisierung und Automatisierung von Prozessschritten sowie der qualitativen Gebrauchtteilbeurteilung und Gebrauchtteilreinigung.
Projektpartner sind die Westfälische Hochschule Gelsenkirchen Bocholt Recklinghausen (Bocholt) und die APS Automotive Product Solutions‐Germany GmbH (Gescher).
AI CAD-Cleaning
Im Projekt soll ein KI-Modell entwickelt werden, mit dem CAD-Rohgeometrien aus 3D-Scans automatisiert bereinigt werden können. Hierdurch soll manueller Aufwand deutlich reduziert werden. Das Modell soll in eine kollaborative B2B-Plattform eingebettet werden, um branchenspezifische Geschäftsmodelle umzusetzen.
Projektpartner sind das Forschungsinstitut für Telekommunikation und Kooperation e.V. (Dortmund), die DigitalTwin Technology GmbH (Köln) und die STURM GmbH (Duisburg).
SmartBMS – Smartes Batteriemanagementsystem und intelligente Datenanalyse im Zellproduktionsprozess
Das Projekt SmartBMS hat das Ziel, das neuartige Verfahren des Eta-Levelings in bestehende Batteriemanagementsysteme zu integrieren. Dabei soll auch validiert werden, welche Steigerung der Produktions- und Betriebseffizienz hierdurch erreicht werden kann. Zudem soll durch die Entwicklung eines Ursache-Wirk-Modells ermittelt werden, inwieweit Toleranzfenster bei der Batteriezellfertigung vergrößert werden können.
Projektpartner sind die Fraunhofer-Einrichtung Forschungsfertigung Batteriezelle FFB (Münster), die Benning Elektrotechnik und Elektronik GmbH & Co. KG (Bocholt), die IconPro GmbH (Aachen), die Albert Seine GmbH (Dülmen) und die PEM Motion GmbH (Aachen).
DeKIBat – Defekterkennung durch die Integration und Verifikation KI-gestützter Multisensorsysteme in der Batteriezellfertigung
Im Projekt soll ein neuartiges, innovatives und auf Thermografie basierendes Prüfsystem für die Beschichtungs- und Trocknungsprozesse in der Elektrodenproduktion entwickelt, erprobt und validiert werden. Hierfür wird zunächst ein umfangreicher Fehlerkatalog entwickelt und ein Lastenheft erarbeitet, um die produkt- und prozessseitigen Anforderungen an das Prüfsystem zu definieren. Anschließend werden physische Grenzmuster in Form von realen Defekten durch gezielte Anpassung der Prozessparameter erzeugt.
Projektpartner sind die Fraunhofer-Einrichtung Forschungsfertigung Batteriezelle FFB (Münster), die RWTH Aachen (Aachen), die BST GmbH (Bielefeld) und die OptiSense GmbH & Co. KG (Haltern am See).
Zum Hintergrund
Für zukunftsweisende, nachhaltige und innovative Vorhaben in Nordrhein-Westfalen stehen aus dem EFRE/JTF-Programm NRW 2021-2027 EU-Mittel in Höhe von 1,9 Milliarden Euro des Europäischen Fonds für Regionale Entwicklung (EFRE) und des Just Transition Funds (JTF) zur Verfügung. Hinzu kommen eine Ko-Finanzierung des Landes Nordrhein-Westfalen und Eigenanteile der Projekte. Unterstützt werden Vorhaben aus den Themenfeldern Innovation, Nachhaltigkeit, Mittelstandsförderung, Lebensqualität, Mobilität, Strukturwandel in Kohlerückzugsregionen sowie strategische Technologien und Wettbewerbsfähigkeit. Weitere Informationen finden Sie unter www.efre.nrw.
Weitere Informationen zum Innovationswettbewerb „Industrie.IN.NRW“ finden Sie unter: https://www.efre.nrw/industrie-in-nrw